Webinars
Bring fresh perspectives on leadership & operational excellence from experienced peers back to your company
Help Everyone Stay Current
Members can benchmark against experienced peers. Ensure your team is continually learning current best practices by watching webinars!
Exclusive to members
Members: $0 – Included with membership!
Non-members: No Access (Become a member)
“We watch webinars as a group and talk about how we use it. They have a greater impact on our team because they come from peers, who are living the same struggles and willing to share what has worked and what hasn’t.”
Stacy Gray, HR Director, American Time
“Webinars have been a fantastic training tool for our company. The topics of the webinars are applicable to anyone within the company, and there’s always great take-aways I can implement in my role.”
Betsy Adams, Human Resources, Agility EMS
PRESENTED BY LEADING MANUFACTURERS
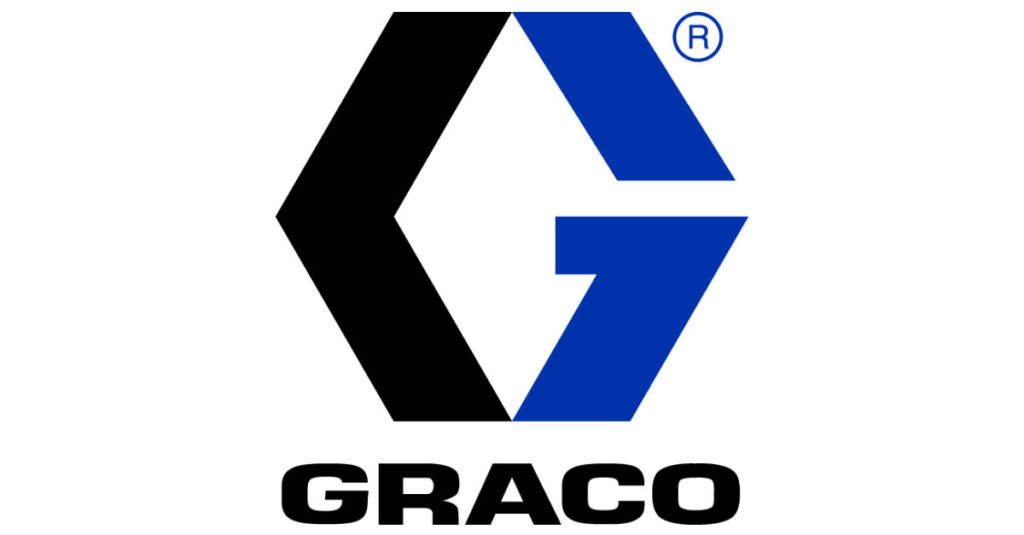
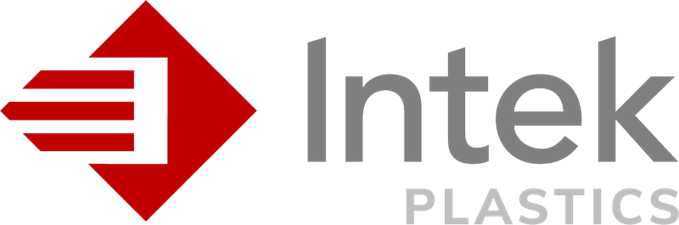
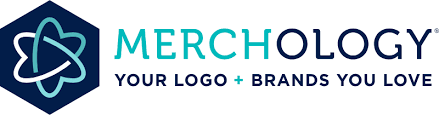
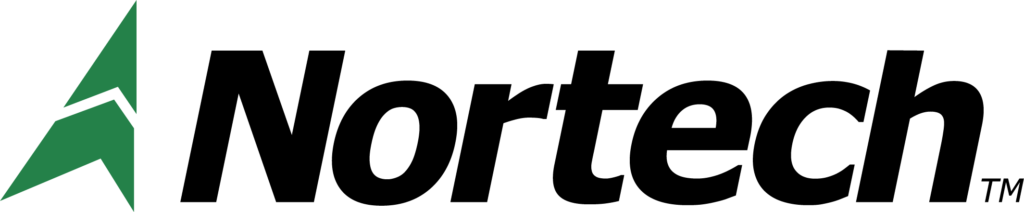
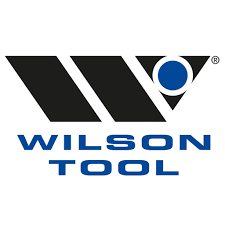
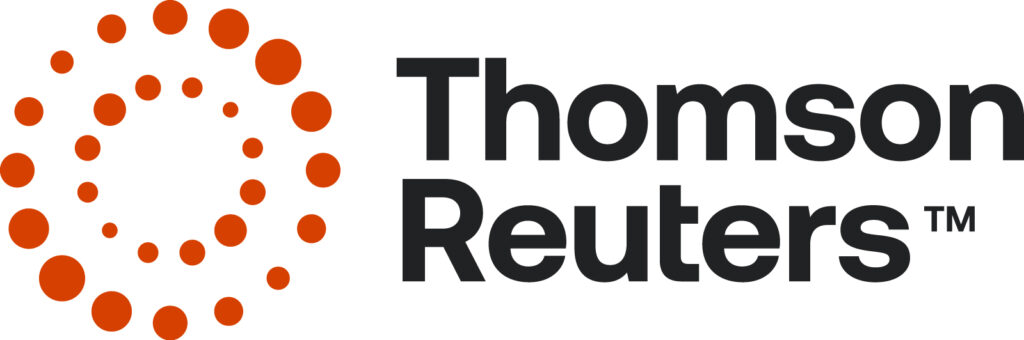
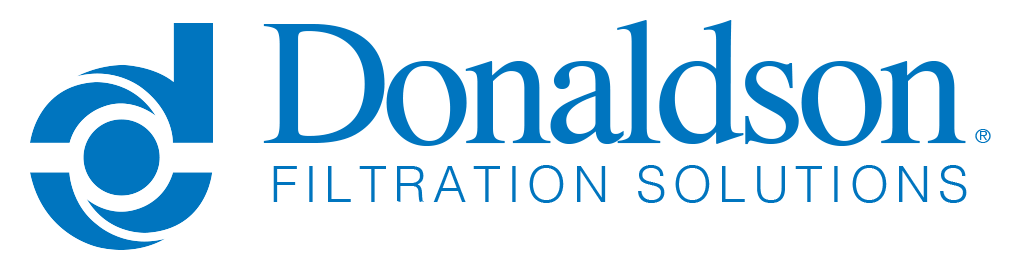
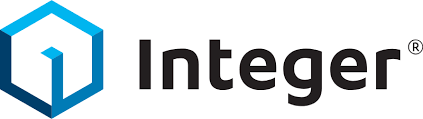
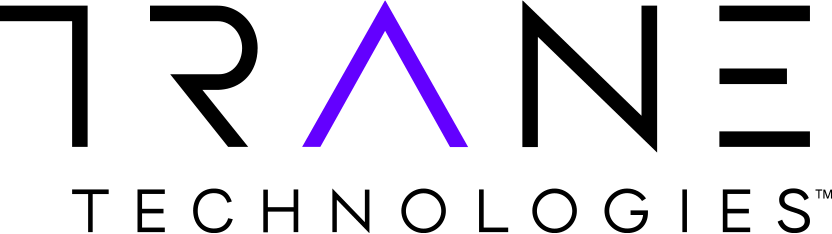
Recent Webinar Topics
- Best In Class One-on-One’s
- Habits Manufacturing Leaders Must Master
- 5S Success
- Leading Organizational Change
- Financial Metrics that Drive Improvement
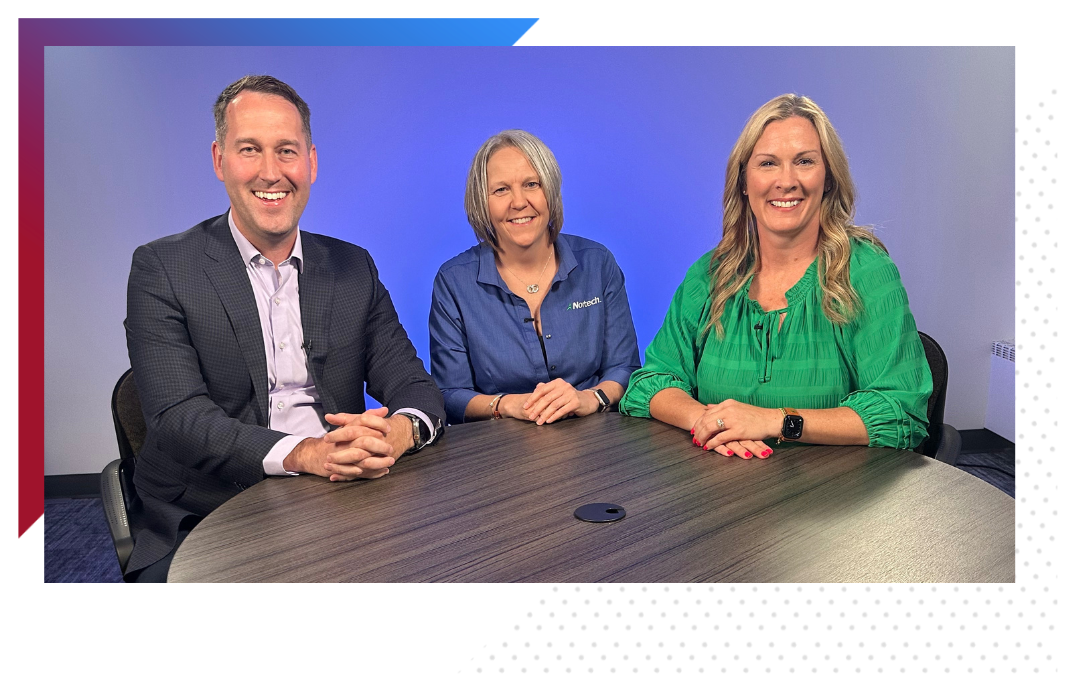
How to Access Webinars
-
Step 1
Become a Member
-
Step 2
Login to your account
-
Step 3
Register for the webinar
-
Step 4
Add more attendees to cart
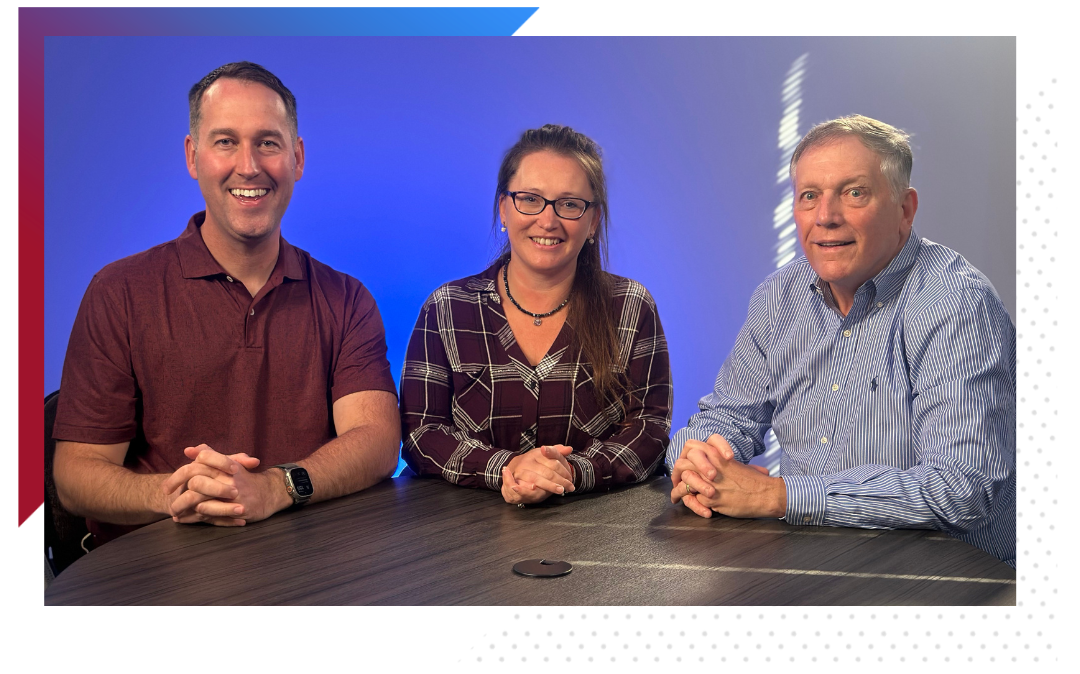
Exclusive to members
New Webinars are broadcasted live once a month and feature experienced manufacturing leaders who share lean, leadership, and HR best practices so you stay current and avoid falling behind or becoming complacent.
Members: $0 – Included with membership!
Non-members: No Access (Become a member)